Components Of Robotics Systems
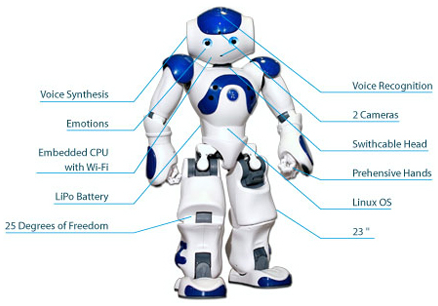
Introduction:
In the world of robotics, actuators play a pivotal role in bringing machines to life. These essential components are responsible for converting electrical energy into mechanical motion, allowing robots to interact with the physical world. Actuators are the muscle of robotic systems, enabling them to perform a wide range of tasks from simple movements to complex operations with precision and efficiency. Let’s delve deeper into the realm of actuators and explore their types, functionalities, and significance in robotics.

Types of Actuators:
- Electric Actuators:
These actuators utilize electrical energy to generate motion. They are commonly found in various robotic applications due to their versatility and ease of control. Electric actuators include servo motors, stepper motors, and DC motors, each serving specific purposes based on the requirements of the robotic system. In the intricate world of robotics, electric actuators stand as fundamental components, orchestrating the graceful dance of machines in response to digital commands. These sophisticated devices harness the power of electricity to translate signals into precise mechanical motion, propelling robots through a myriad of tasks with finesse and efficiency. Electric actuators are the silent heroes behind the seamless movements of robotic arms, the agile locomotion of drones, and the delicate manipulations of surgical robots. Let us embark on a journey into the realm of electric actuators, unraveling their types, functionalities, and pivotal role in shaping the landscape of modern robotics.
Types of Electric Actuators:
- Servo Motors:
Servo motors reign supreme as the workhorses of robotics, offering unparalleled precision, torque, and control. These compact yet powerful motors utilize feedback mechanisms such as encoders to maintain accurate positioning and velocity, making them indispensable in applications demanding high levels of accuracy and repeatability. From robotic arms in manufacturing to autonomous vehicles on the road, servo motors drive the heartbeat of countless robotic systems with unwavering reliability.
- Stepper Motors:
Stepper motors, with their distinctive step-by-step motion, excel in applications requiring precise positioning and open-loop control. These motors advance in discrete increments, allowing for precise control over rotation angles and speeds. Stepper motors find widespread use in 3D printers, CNC machines, and robotic systems where simplicity, cost-effectiveness, and positional accuracy are paramount.
- DC Motors:
Direct current (DC) motors offer simplicity and versatility, making them a popular choice in robotics for a wide range of applications. These motors operate on the principle of electromagnetic induction, converting electrical energy into rotational motion. DC motors come in various configurations, including brushed and brushless variants, each offering unique advantages in terms of cost, efficiency, and maintenance requirements. From mobile robots to robotic prosthetics, DC motors provide the driving force behind a myriad of robotic endeavors.
- Linear Actuators:
Linear actuators translate electrical energy into linear motion, enabling robots to perform tasks such as lifting, pushing, and pulling with precision. These actuators come in different forms, including lead screw actuators, belt-driven actuators, and linear motors, each tailored to specific applications based on factors such as load capacity, speed, and stroke length. Linear actuators find applications in robotics ranging from automated assembly lines to medical devices, where linear motion is essential for task execution.
- Voice Coil Actuators:
Voice coil actuators, also known as linear motors, offer high-speed and high-precision linear motion without the need for mechanical commutation. These actuators consist of a coil suspended within a magnetic field, with the application of current inducing motion along the axis of the coil. Voice coil actuators excel in applications requiring rapid and precise positioning, such as laser machining systems, semiconductor manufacturing equipment, and dynamic control systems.
Functionalities of Electric Actuators:
- Motion Control:
Electric actuators serve as the primary means of generating motion in robotic systems, enabling robots to move their limbs, joints, or end-effectors with precision and agility. Whether executing complex trajectories in industrial assembly lines or navigating obstacle-laden environments in autonomous vehicles, electric actuators provide the mechanical muscle needed to bring robotic motions to life.
- Positioning and Accuracy:
Electric actuators excel in providing precise positioning and accurate motion control, essential for tasks requiring fine manipulation and coordination. Through feedback mechanisms such as encoders and sensors, these actuators maintain precise position, velocity, and torque control, ensuring consistency and repeatability in robotic operations. From pick-and-place tasks in logistics to surgical procedures in healthcare, accurate positioning facilitated by electric actuators underpins the success of diverse robotic applications.
- Speed and Agility:
Electric actuators offer rapid response times and dynamic performance, enabling robots to swiftly adapt to changing environments and execute tasks with agility. Whether performing high-speed maneuvers in robotic sports competitions or navigating complex terrain in search-and-rescue missions, electric actuators empower robots with the speed and agility needed to excel in dynamic and unpredictable scenarios.
- Efficiency and Energy Optimization:
Electric actuators are designed to operate with efficiency and energy optimization in mind, maximizing output power while minimizing energy consumption. Through advancements in motor design, control algorithms, and power electronics, modern electric actuators achieve high levels of efficiency across a wide range of operating conditions. By optimizing energy usage, these actuators contribute to the overall sustainability and autonomy of robotic systems, extending their operational capabilities in resource-constrained environments.
- Integration and Interfacing:
Electric actuators seamlessly integrate with control systems and interfaces, enabling intuitive interaction and seamless communication between humans and robots. Through standardized protocols such as Modbus, CAN bus, and EtherCAT, electric actuators interface with programmable logic controllers (PLCs), microcontrollers, and human-machine interfaces (HMIs), facilitating real-time monitoring, control, and diagnostics. This interoperability fosters collaboration and interoperability within robotic ecosystems, enabling the seamless integration of actuators into diverse applications and industries.
Significance of Electric Actuators in Robotics:
- Precision and Reliability:
Electric actuators play a crucial role in ensuring precision and reliability in robotic operations, underpinning the success of tasks requiring accuracy and repeatability. Whether performing delicate surgical procedures or executing precise assembly tasks in manufacturing, electric actuators provide the mechanical precision needed to achieve consistent and reliable outcomes.
- Versatility and Adaptability:
The versatility and adaptability of electric actuators enable robots to tackle a wide range of tasks and environments with ease. From industrial automation to service robotics, electric actuators empower robots with the flexibility to adapt their motions and interactions to diverse scenarios, enhancing their utility across various applications and industries.
- Innovation and Advancement:
Ongoing research and development in electric actuator technologies drive innovation and advancement in the field of robotics, pushing the boundaries of what robots can achieve. From advancements in motor design and control algorithms to the integration of smart sensors and materials, electric actuators continue to evolve, unlocking new possibilities for robotic applications in fields such as healthcare, transportation, and exploration.
- Safety and Efficiency:
Electric actuators contribute to the safety and efficiency of robotic systems through features such as overload protection, fault detection, and energy optimization. By implementing safety mechanisms and energy-efficient designs, electric actuators minimize the risk of accidents and malfunctions while maximizing the productivity and longevity of robotic systems, ensuring safe and sustainable operation in diverse environments.
- Empowerment and Collaboration:
Electric actuators empower humans to interact and collaborate with robots in a variety of contexts, from industrial manufacturing to assistive technologies. By providing intuitive interfaces and seamless integration with human-operated control systems, electric actuators facilitate collaboration between humans and robots, unlocking new opportunities for enhanced productivity, creativity, and innovation.
In conclusion, electric actuators stand as indispensable components in the realm of robotics, driving the motion, precision, and versatility of robotic systems across diverse applications and industries. From servo motors orchestrating the graceful movements of industrial robots to stepper motors powering the intricate motions of 3D printers, electric actuators play a pivotal role in shaping the evolution of robotics, enabling machines to transcend boundaries and redefine the possibilities of human-machine collaboration. As robotics continues to advance and proliferate into new domains, the significance of electric actuators as catalysts for innovation and progress remains unwavering, paving the way for a future where robots seamlessly integrate into every facet of our lives, enriching and empowering humanity with their boundless potential.
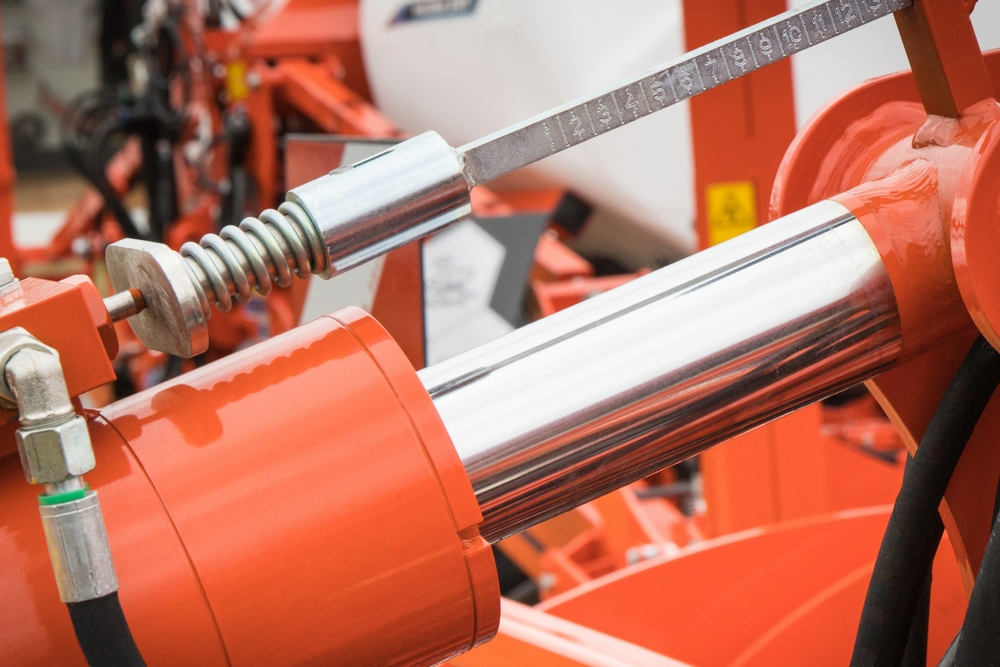
Hydraulic Actuators:
Hydraulic actuators utilize pressurized fluid to produce mechanical motion. They are known for their high force output, making them suitable for heavy-duty applications such as industrial automation and construction robotics. Hydraulic cylinders and hydraulic motors are examples of hydraulic actuators widely used in robotics.
Types of Hydraulic Actuators:
- Hydraulic Cylinders:
Hydraulic cylinders are the quintessential workhorses of hydraulic actuators, converting fluid pressure into linear motion with exceptional force and precision. These cylinders consist of a piston enclosed within a cylindrical chamber filled with hydraulic fluid. When pressurized, the fluid exerts force on the piston, causing it to move along the cylinder’s axis. Hydraulic cylinders come in various configurations, including single-acting, double-acting, and telescopic, each tailored to specific applications based on factors such as stroke length, load capacity, and speed requirements.
- Hydraulic Motors
Hydraulic motors harness the power of hydraulic pressure to drive rotational motion, making them ideal for applications requiring high torque and low-speed operation. These motors operate on the principle of fluid flow through a series of chambers or vanes, exerting torque on a shaft connected to the load. Hydraulic motors come in different designs, including gear, vane, and piston types, each offering unique advantages in terms of efficiency, speed, and power output. From heavy-duty machinery in construction to propulsion systems in marine vessels, hydraulic motors provide the driving force behind a myriad of robotic applications.
- Hydraulic Valves:
Hydraulic valves serve as the control center of hydraulic systems, regulating the flow, direction, and pressure of hydraulic fluid to achieve precise and dynamic motion control. These valves come in various configurations, including directional control valves, pressure control valves, and flow control valves, each playing a critical role in orchestrating the movements of hydraulic actuators. Hydraulic valves enable robots to perform complex maneuvers, synchronize multiple actuators, and respond dynamically to changing environmental conditions, enhancing their versatility and adaptability in diverse applications.
- Functionalities of Hydraulic Actuators:
- Force Generation:
Hydraulic actuators excel in generating immense force, making them indispensable for tasks requiring heavy lifting, pushing, or pulling. By harnessing the power of pressurized fluid, hydraulic actuators can exert forces far beyond the capabilities of electric or pneumatic actuators, enabling robots to tackle large-scale industrial tasks with ease. Whether lifting heavy payloads in material handling systems or exerting crushing force in hydraulic presses, hydraulic actuators provide the muscle needed to conquer formidable challenges in robotics.
- Precision and Control:
Despite their formidable power, hydraulic actuators offer precise control over motion, enabling robots to execute delicate maneuvers with finesse. Through sophisticated feedback and control systems, hydraulic actuators can achieve precise positioning, velocity, and force control, ensuring accuracy and repeatability in robotic operations. Whether performing intricate assembly tasks in manufacturing or navigating complex terrain in off-road vehicles, hydraulic actuators provide the precision needed to accomplish tasks with surgical precision.
- Adaptability and Flexibility:
Hydraulic actuators exhibit remarkable adaptability and flexibility, allowing robots to adjust their motions and interactions to changing task requirements or environmental conditions. By modulating fluid flow, pressure, and direction, hydraulic actuators can adapt their behavior in real-time, enabling robots to respond dynamically to unforeseen obstacles, variations in load, or changes in terrain. This adaptability is particularly valuable in applications such as agricultural machinery, where robots must navigate unpredictable terrain and interact with diverse objects while maintaining optimal performance.
- Durability and Reliability:
Hydraulic actuators are renowned for their durability and reliability, capable of withstanding harsh operating conditions and heavy loads with minimal maintenance. Unlike electric actuators, which may be susceptible to overheating or mechanical wear, hydraulic actuators operate smoothly and reliably over extended periods, making them ideal for continuous-duty applications in industrial automation, construction, and mining. The robust construction and simplicity of hydraulic actuators contribute to their longevity and resilience, ensuring uninterrupted operation in demanding environments.
- Safety and Stability:
Hydraulic actuators prioritize safety and stability in robotic operations, employing fail-safe mechanisms and overload protection systems to prevent accidents and ensure operator safety. By incorporating pressure relief valves, check valves, and accumulator systems, hydraulic actuators mitigate the risk of hydraulic system failures, hydraulic fluid leaks, or sudden load shifts, enhancing the safety and stability of robotic systems. This reliability and predictability are essential for applications such as aerial work platforms, where human operators rely on hydraulic actuators to maintain stable and secure platforms at height.
Significance of Hydraulic Actuators in Robotics:
- Power and Performance:
Hydraulic actuators play a crucial role in enhancing the power and performance of robotic systems, enabling them to tackle tasks beyond the capabilities of other actuation technologies. Whether lifting heavy loads, exerting high forces, or operating in harsh environments, hydraulic actuators provide the muscle needed to achieve superior performance in industrial automation, construction, and heavy machinery applications.
- Versatility and Adaptability:
The versatility and adaptability of hydraulic actuators empower robots to operate in diverse environments and perform a wide range of tasks with precision and efficiency. From lifting and positioning in manufacturing to excavation and material handling in construction, hydraulic actuators enable robots to adapt their motions and interactions to varying task requirements, enhancing their utility across different industries and applications.
- Efficiency and Sustainability:
Despite their reputation for power, hydraulic actuators can also be efficient and sustainable when properly designed and optimized. By leveraging advanced hydraulic systems, energy-efficient pumps, and regenerative braking technologies, hydraulic actuators can minimize energy consumption and environmental impact while maximizing performance and productivity. This balance of power and efficiency is essential for promoting sustainability and resource conservation in robotics.
- Innovation and Advancement:
Ongoing research and development in hydraulic actuator technologies drive innovation and advancement in the field of robotics, paving the way for new applications and capabilities. From advancements in fluid dynamics and materials science to integration with advanced control algorithms and sensing systems, hydraulic actuators continue to evolve, unlocking new possibilities for robotic automation in areas such as renewable energy, underwater exploration, and disaster response.
- Collaboration and Integration:
Hydraulic actuators foster collaboration and integration within robotic ecosystems, enabling seamless interaction and interoperability between robots and other automation systems. By providing standardized interfaces, communication protocols, and interoperable components, hydraulic actuators facilitate the integration of robots into existing industrial processes, supply chains, and infrastructure networks, driving efficiency, productivity, and innovation across various sectors.
In conclusion, hydraulic actuators stand as indispensable components in the realm of robotics, offering unmatched power, precision, and reliability for a wide range of applications and industries. From heavy lifting in manufacturing to agile maneuvering in construction, hydraulic actuators empower robots to conquer challenges with confidence and efficiency, shaping the future of automation and human-machine collaboration. As robotics continues to advance and diversify, the significance of hydraulic actuators as catalysts for innovation and progress remains steadfast, driving the evolution of robotic systems towards new frontiers of performance, versatility, and sustainability.

- Pneumatic Actuators:
Pneumatic actuators utilize compressed air to generate motion. They are lightweight, cost-effective, and ideal for applications requiring rapid movements and moderate force. Pneumatic actuators are commonly used in robotics for tasks such as gripping, lifting, and positioning.
Types of Pneumatic Actuators:
- Pneumatic Cylinders:
Pneumatic cylinders serve as the backbone of pneumatic actuation systems, converting compressed air into linear motion with remarkable efficiency and speed. These cylinders consist of a piston enclosed within a cylindrical chamber, with compressed air acting upon the piston to generate linear force. Pneumatic cylinders come in various configurations, including single-acting, double-acting, and rotary types, each tailored to specific applications based on factors such as stroke length, load capacity, and speed requirements.
- Pneumatic Rotary Actuators:
Pneumatic rotary actuators enable rotational motion in pneumatic systems, offering precise control and high torque output. These actuators utilize the power of compressed air to drive rotary motion, allowing robots to perform tasks such as turning, gripping, and positioning with agility and accuracy. Pneumatic rotary actuators find applications in robotic arms, industrial manipulators, and automated machinery, where rotational motion is essential for task execution.
- Pneumatic Grippers:
Pneumatic grippers facilitate the manipulation and handling of objects in robotic systems, providing a secure and versatile means of grasping and releasing items of varying shapes and sizes. These grippers employ pneumatic pressure to actuate jaws or fingers, allowing robots to grip, lift, and transport objects with precision and efficiency. Pneumatic grippers come in different designs, including parallel, angular, and three-finger configurations, each optimized for specific gripping tasks in industries such as manufacturing, logistics, and assembly.
- Pneumatic Slides:
Pneumatic slides enable linear motion in pneumatic systems, providing a smooth and reliable means of positioning and actuation. These slides utilize compressed air to drive linear motion along a guided path, allowing robots to perform tasks such as pushing, pulling, and indexing with precision and repeatability. Pneumatic slides find applications in automated assembly lines, packaging machinery, and material handling systems, where linear motion is critical for task execution and throughput optimization.
- Pneumatic Vacuum Generators:
Pneumatic vacuum generators harness the power of differential pressure to create suction force, enabling robots to grip and manipulate non-porous objects without physical contact. These generators utilize compressed air to create a vacuum within a chamber, causing atmospheric pressure to exert force on objects, securing them in place. Pneumatic vacuum generators are commonly used in pick-and-place applications, packaging systems, and robotic end-effectors, where non-contact gripping is essential for delicate or fragile objects.
Functionalities of Pneumatic Actuators:
- Speed and Agility:
Pneumatic actuators offer rapid response times and dynamic performance, enabling robots to execute tasks with agility and efficiency. Due to the compressibility of air and the absence of complex mechanical components, pneumatic actuators can achieve high speeds and accelerations, making them ideal for applications requiring rapid motion and quick cycle times. Whether performing pick-and-place operations in manufacturing or navigating obstacle-laden environments in mobile robotics, pneumatic actuators empower robots with the speed and agility needed to excel in dynamic and fast-paced environments.
- Force and Power:
Despite their lightweight and compact design, pneumatic actuators can generate significant force and power, making them suitable for a wide range of lifting, pushing, and gripping tasks. By varying the pressure and volume of compressed air, pneumatic actuators can exert force proportional to the load requirements, enabling robots to manipulate objects of varying weights and sizes with ease. From lifting heavy payloads in material handling systems to clamping workpieces in machining operations, pneumatic actuators provide the muscle needed to accomplish diverse tasks in robotics.
- Precision and Control:
Pneumatic actuators offer precise control over motion and force, allowing robots to execute tasks with accuracy and repeatability. Through the use of precision valves, regulators, and sensors, pneumatic systems can modulate air pressure, flow rates, and actuation forces with fine granularity, ensuring precise positioning and motion control. Whether maintaining tight tolerances in manufacturing processes or executing delicate maneuvers in robotic surgery, pneumatic actuators enable robots to achieve consistent and reliable performance in a wide range of applications.
- Simplicity and Reliability:
Pneumatic actuators are characterized by their simplicity and reliability, making them ideal for rugged and demanding environments. Unlike electromechanical actuators, which may be prone to mechanical wear or electrical failures, pneumatic actuators operate without the need for complex components such as motors, gears, or bearings. This simplicity reduces the risk of downtime and maintenance costs, ensuring uninterrupted operation in industrial automation, mobile robotics, and harsh operating conditions.
- Flexibility and Adaptability:
Pneumatic actuators offer inherent flexibility and adaptability, allowing robots to perform a wide range of tasks and maneuvers with minimal adjustments or reconfiguration. By modulating air pressure, flow rates, and actuation parameters, pneumatic systems can adapt their behavior to changing task requirements or environmental conditions, enabling robots to respond dynamically to unforeseen obstacles, variations in load, or changes in terrain. This flexibility is particularly valuable in applications such as assembly automation, where robots must accommodate diverse product configurations and production schedules while maintaining optimal performance.
Significance of Pneumatic Actuators in Robotics:
- Efficiency and Energy Optimization:
Pneumatic actuators are known for their efficiency and energy optimization, leveraging the compressibility of air to achieve high power output with minimal energy consumption. By utilizing energy-efficient components such as pneumatic valves, regulators, and actuators, pneumatic systems can maximize energy transfer and minimize losses, ensuring optimal performance and sustainability in robotic operations. This energy efficiency is essential for reducing operational costs and environmental impact, particularly in applications such as manufacturing, where energy consumption is a significant factor in production efficiency.
- Safety and Compliance:
Pneumatic actuators prioritize safety and compliance in robotic operations, incorporating safety features such as pressure relief valves, flow restrictors, and emergency stop systems to prevent accidents and ensure operator safety. By implementing fail-safe mechanisms and interlocks, pneumatic systems can mitigate the risk of overloading, leakage, or sudden actuator failure, enhancing the safety and reliability of robotic operations in industrial, medical, and hazardous environments. This focus on safety and compliance is critical for regulatory compliance and risk management in robotics, ensuring the protection of human operators and assets.
- Cost-Effectiveness and Scalability:
Pneumatic actuators offer cost-effective solutions for robotic automation, providing high performance and reliability at a competitive price point. Compared to electromechanical actuators or hydraulic systems, pneumatic actuators require less complex infrastructure, maintenance, and operational costs, making them an attractive option for small to medium-sized enterprises (SMEs) and emerging industries. Additionally, pneumatic systems are scalable and modular, allowing for easy integration and expansion as robotic applications evolve and grow in complexity. This cost-effectiveness and scalability enable pneumatic actuators to play

- Piezoelectric Actuators:
Piezoelectric actuators employ the piezoelectric effect to generate motion when subjected to an electric field. They are known for their high precision and responsiveness, making them suitable for micro-manipulation tasks in fields like biomedical robotics and nanotechnology.
Types of Piezoelectric Actuators:
- Piezoelectric Stack Actuators:
Piezoelectric stack actuators are among the most common types of piezoelectric actuators, consisting of multiple layers of piezoelectric material sandwiched between electrodes. When an electric field is applied across the stack, the piezoelectric layers expand or contract, generating mechanical displacement along the axis of the stack. These actuators offer high precision and displacement capabilities, making them ideal for applications requiring nanoscale positioning and fine motion control, such as scanning probe microscopy and optical alignment systems.
- Piezoelectric Tube Actuators:
Piezoelectric tube actuators utilize the radial expansion or contraction of a cylindrical piezoelectric tube to generate linear motion. By applying an electric field to the inner or outer surface of the tube, the piezoelectric material expands or contracts, causing the tube to elongate or contract along its axis. Piezoelectric tube actuators offer high force output and displacement, making them suitable for applications such as microfluidics, valve control, and precision machining, where linear motion and force are critical for task execution.
- Piezoelectric Benders and Flexures:
Piezoelectric benders and flexures utilize the bending or flexing motion of piezoelectric elements to generate mechanical displacement. These actuators consist of thin piezoelectric strips or beams bonded to a flexible substrate, allowing them to bend or flex in response to an applied electric field. Piezoelectric benders and flexures offer high speed and precision, making them suitable for applications such as adaptive optics, active vibration damping, and micro-robotics, where rapid response and precise control are essential for performance.
- Piezoelectric Resonators:
Piezoelectric resonators leverage the resonance phenomenon of piezoelectric materials to generate mechanical vibration or oscillation. These actuators consist of piezoelectric elements bonded to a resonant structure, such as a cantilever or tuning fork, which vibrates at a specific frequency when subjected to an electric field. Piezoelectric resonators find applications in areas such as ultrasonic cleaning, ultrasonic welding, and acoustic wave devices, where mechanical vibration or oscillation is utilized for material processing, sensing, or actuation.
- Piezoelectric Motors:
Piezoelectric motors utilize the piezoelectric effect to drive rotational or linear motion without the need for traditional mechanical components such as gears or bearings. These motors operate by inducing frictional or contact forces between piezoelectric elements and a moving platform, causing it to translate or rotate with high precision and resolution. Piezoelectric motors are used in applications such as precision optics, micro-positioning stages, and nanopositioning systems, where compact size, low inertia, and precise motion control are required.
Functionalities of Piezoelectric Actuators:
- Precision Positioning:
Piezoelectric actuators offer unparalleled precision in positioning, enabling robots to achieve sub-micron and nanometer-level accuracy in motion control. The inherent stiffness and responsiveness of piezoelectric materials allow for rapid and precise displacement, making them ideal for applications requiring fine adjustment, alignment, or scanning. Whether performing microscopy, lithography, or optical alignment, piezoelectric actuators provide the precise positioning needed to achieve high-resolution imaging, patterning, and alignment in robotics.
- Fast Response Time:
Piezoelectric actuators exhibit rapid response times, enabling robots to execute dynamic motions and rapid adjustments with minimal delay. The direct coupling between electrical input and mechanical output in piezoelectric materials allows for millisecond-level response times, making them ideal for applications requiring fast actuation, feedback, or modulation. Whether compensating for dynamic disturbances, tracking fast-moving targets, or adjusting for environmental changes, piezoelectric actuators ensure rapid and responsive performance in robotics.
- High Force and Power Density:
Despite their compact size, piezoelectric actuators offer high force and power density, enabling robots to exert significant forces and torques in confined spaces. The electromechanical coupling efficiency of piezoelectric materials allows for efficient energy conversion and transmission, resulting in high force output per unit volume or weight. Whether gripping objects, manipulating tools, or driving mechanisms, piezoelectric actuators provide the high force and power density needed to accomplish tasks with precision and efficiency in robotics.
- Low Power Consumption:
Piezoelectric actuators are known for their low power consumption, making them energy-efficient solutions for robotic systems. The direct conversion of electrical energy into mechanical displacement in piezoelectric materials minimizes energy losses and wasted power, resulting in efficient actuation with minimal heat generation or dissipation. Whether operating in battery-powered devices, portable instruments, or energy-constrained environments, piezoelectric actuators offer low power consumption and prolonged battery life, enhancing the autonomy and sustainability of robotic systems.
- Non-Magnetic and Non-Conductive Properties:
Piezoelectric actuators exhibit non-magnetic and non-conductive properties, making them suitable for use in environments where magnetic interference or electrical conductivity is a concern. Unlike electromagnetic actuators or motors, which may be susceptible to electromagnetic interference (EMI) or magnetic field effects, piezoelectric actuators are immune to magnetic fields and do not generate electromagnetic radiation. This non-magnetic and non-conductive nature makes piezoelectric actuators ideal for applications such as magnetic resonance imaging (MRI), semiconductor manufacturing, and precision instrumentation, where electromagnetic compatibility (EMC) and material purity are critical considerations.
Significance of Piezoelectric Actuators in Robotics:
- Enhanced Precision and Accuracy:
Piezoelectric actuators play a crucial role in enhancing the precision and accuracy of robotic systems, enabling them to perform tasks with sub-micron and nanometer-level resolution. Whether positioning components in semiconductor fabrication, aligning optics in laser systems, or scanning surfaces in microscopy, piezoelectric actuators provide the precise motion control needed to achieve high-resolution imaging, patterning, and manipulation in robotics.
- Dynamic and Responsive Motion:
Piezoelectric actuators enable robots to execute dynamic and responsive motions with rapid adjustments and precise control. The fast response times and high bandwidth of piezoelectric materials allow for real-time modulation and adaptation to changing task requirements or environmental conditions. Whether tracking fast-moving targets, compensating for dynamic disturbances, or adjusting for variations in load or friction, piezoelectric actuators ensure dynamic and responsive performance in robotics.
- Miniaturization and Integration:
Piezoelectric actuators facilitate miniaturization and integration in robotic systems, allowing for compact and lightweight designs with high performance and efficiency. The small size, low weight, and high power density of piezoelectric actuators enable
Functionalities of Actuators:
- Motion Generation:
The primary function of actuators is to generate mechanical motion, enabling robots to move their limbs, joints, or end-effectors to perform tasks. Depending on the type of actuator and its design, motion can be achieved through rotational, linear, or oscillatory movements.
- Force and Torque Generation:
Actuators provide the necessary force and torque required to overcome resistance and manipulate objects in the robot’s environment. The force output of an actuator determines its capability to lift, push, pull, or manipulate objects of varying weights and sizes.
- Control and Feedback:
Actuators are equipped with sensors and feedback mechanisms to ensure precise control of motion and interaction with the environment. Feedback from sensors such as encoders and accelerometers allows the robotic system to monitor the position, velocity, and force exerted by the actuators, enabling closed-loop control for accurate and stable operation.
- Adaptability and Flexibility:
Actuators can be designed to exhibit adaptive and flexible behavior, allowing robots to adjust their movements and interactions based on changes in the environment or task requirements. This adaptability is essential for robots operating in dynamic and unstructured environments where conditions may vary unpredictably.
- Energy Efficiency:
Efficient utilization of energy is crucial for the performance and autonomy of robotic systems. Actuators are designed to minimize energy consumption while maximizing output power, ensuring optimal efficiency in various operating conditions. Advancements in actuator technologies, such as brushless motors and smart materials, contribute to enhanced energy efficiency in robotics.
Significance of Actuators in Robotics:
- Functionality and Performance:
Actuators are essential for enabling the functionality and performance of robotic systems. They determine the range of motions, speed, accuracy, and payload capacity of robots, influencing their capabilities across different applications and industries.
- Versatility and Adaptability:
The diverse range of actuators available allows robotic designers to select the most suitable type for specific tasks and environments. Whether it’s precise positioning in manufacturing processes or agile locomotion in mobile robots, actuators provide the necessary versatility and adaptability to meet varied requirements.
- Productivity and Efficiency:
Actuators play a crucial role in enhancing productivity and efficiency in industrial automation and manufacturing processes. By automating repetitive tasks and operating with precision and speed, robots equipped with efficient actuators can improve production throughput, quality, and consistency while reducing labor costs and cycle times.
- Safety and Reliability:
Reliable actuation systems are essential for ensuring the safety of robotic operations, particularly in collaborative and human-robot interaction scenarios. Actuators with built-in safety features, such as overload protection and fail-safe mechanisms, contribute to the overall reliability and integrity of robotic systems, minimizing the risk of accidents and malfunctions.
- Innovation and Advancement:
Ongoing research and development in actuator technologies drive innovation and advancement in the field of robotics. From novel materials and manufacturing techniques to advanced control algorithms and integrated sensing systems, advancements in actuators continue to push the boundaries of what robots can achieve, opening up new possibilities for applications in diverse domains.
In conclusion, actuators form the backbone of robotic systems, enabling them to translate electrical signals into mechanical motion and perform a myriad of tasks with precision, efficiency, and versatility. As robotics continues to evolve and expand into new frontiers, the role of actuators remains indispensable in shaping the future of automation, artificial intelligence, and human-machine interaction.
